GreCon CS 5000
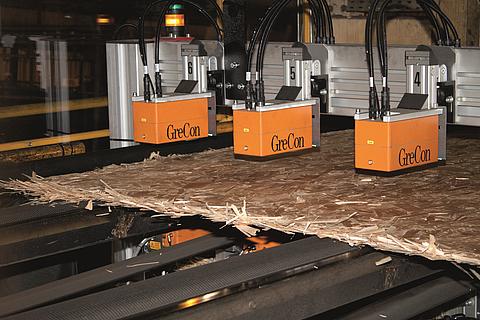
BENEFITS AT A GLANCE
-
- Prevent manufacturing faulty panel weights
- Monitoring of material distribution and panel weight on a continuous basis
- Installation in limited space conditions possible (e.g. press extensions)
- Saving of the weighing table
- Assurance of product quality and material consumption optimization
- Ideal for high production speeds
- Calibration with homogeneous test samples allows precise measurements
- No dependence on the tare – ideal for thin plates
MEASURING METHOD
-
The continuous board scale operates in a non-contact way. For measurement, the material to be weighed is penetrated by X-rays. Depending on the material quantity and the specific weight of the material, the radiation intensity measured by the sensor changes. This is the measure for the weight per unit area (kg/m²).
SOFTWARE FUNCTIONS AND VISUALISATION
-
The visualisation is the core of the software. The recorded measuring data is collected, registered and graphically processed. The easy menu structure which is adapted to all measuring systems makes an intuitive and user-friendly operation possible.
The ergonomically designed software based on the Windows operating system allows an easy handling of the system by the operator. The recorded measured values are processed and displayed in a clearly structured way.
Thanks to the visualisation software in modular design, the system can be adapted to your requirements so that the operation of the plant with different applications is possible. Furthermore the surface of the visualisation software can be compiled according to your needs.
-
The system can be adapted optimally to the different requirements via recipes. The structure of the recipe management is very easy. The input of the panel-specific data enables the operator to start the measurement with only few mouse clicks. The start of a measurement and the necessary selection of a recipe make the integration of the measurement system into the process chain possible.
All default values of a production type are saved in the recipe management. Besides the production parameters, as e.g.
- panel thickness
- panel width
- panel length
- raw density
- tolerances
also all measuring-specific parameters are filed under the production type. When the production type is loaded again, all necessary parameters are available again.
-
The control software takes over all tasks which are necessary for the proper operation of the system:
- Inspection of the measuring sensors by means of a reference sample with tolerance monitoring
-
The system can be adapted optimally to the different requirements via recipes. The structure of the recipe management is very easy. The input of the panel-specific data enables the operator to start the measurement with only few mouse clicks. The start of a measurement and the necessary selection of a recipe make the integration of the measurement system into the process chain possible.
All default values of a production type are saved in the recipe management. Besides the production parameters, as e.g.
- panel thickness
- panel width
- panel length
- raw density
- tolerances
also all measuring-specific parameters are filed under the production type. When the production type is loaded again, all necessary parameters are available again
-
- Any panel data is stored in an SQL data base together with the recipe parameters and the measuring results.
- Display of the position and the scope of the violated tolerances of historical panels.
- Easy search function via date and time.
- Export of panel data.
-
Individual time-relevant reports as e.g. the shift and month reports can be generated from the data base.
The graphic presently shown on the screen can be printed out by pressing a button. Furthermore it is possible to print out a numerical report in case of a change of the production types or the shift.
It is possible to generate different reports automatically and store or print them, as for example:
- shift report
- type report
- graphic report
Furthermore it is possible to print out a screen shot of the history for statistical purposes. The data can also be exported from the history management in the standard file format XLS.
APPLICATIONS
-
- Wood based panels: before or after cross cut saw
- Electrical insulation material (transformer board): after the press
- Insulating Material: hot end cold
- Machine car parts: after the press
-
Supply voltage 230 V ± 10 % / 110 V ± 10 % Frequency 50 Hz / 60 Hz Mains type Phase/neutral conductor/protective conductor Power consumption 500 VA Compressed air supply 6 bar (precleaned, max. temperature: 25 °C) Compressed air consumption 150 l/min -
Places of installation (other places of installation on request) Holzwerkstoffe: vor oder nach der Aufteilsäge, Dämmstoffe: hot end oder cold end, Elektroisolierstoffe (Trafoboard): nach der Presse Ambient temperature 5 to 45 °C Relative humidity non-condensing Protection class IP54 -
Type of material Holzwerkstoffe, Dämmstoffe, Elektroisolierstoffe (Trafoboard) Material/panel size max. 4000 mm Material/panel thickness max. 40 mm Transport speed max. 240 m/min -
Number max. 10 simultaneously Measuring process (see product finder) X-ray Measuring range 2 to 40 kg/m² Repeat accuracy (in case of constant environmental conditions) ± 10 g/m² (± 1 σ) Resolution (diameter of the measured spot) 10 g/m2 Minimum distance between two sensors 360 mm -
- OPC
- Digital I/O
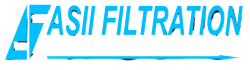