GreCon LENGTHCONTROL
The measuring system LENGTHCONTROL determines the length and the speed of solid, soft and moist materials by recording the measured value without contact with laser beams. The optimization of the documentation and control processes for our customers is in the focus when the length measuring system is used. However, also material costs by reduction of the cutting scrap are saved. For example, a too long board means too high material and production costs for the manufacturer, even if the board is still acceptable for the customer. Thanks to the 100% measurement of the board length, cutting by a diagonal or dividing saw is monitored and continuously corrected.
Exact graphical and numerical displays make a timely intervention of the operator into the cutting process possible. A uniform board quality and an optimal use of material and energy can be achieved.
The measured values can be recorded up to the edges of the material. Depending on the requirements, the lengths and the speed can be determined at panel-shaped products or even in case of the endless application.
The GreCon LENGTHCONTROL is the ideal solution especially in case of production systems with a very high throughput speed, with confined space conditions or in case of an unfavorable ratio between board length and speed. In addition, the average density can be determined and used for process optimization by an optimal connection to a GreCon thickness gauge.
BENEFITS AT A GLANCE
MEASURING METHOD
LENGTHCONTROL uses the double beam interferometer technology for precise measurements of the speed.The measured speed determines the length of the moving parts via the time. The beam is split and intersects in the room.The two transverse beams interact forming a border pattern which is orthogonal to the plane of the two beams.The light is scattered if the material runs through the measuring zone. This scattered light is detected by the measuring unit and converted into electrical signals. The frequency of the electrical signal includes information on the speed of the material. The signal processor converts the electrical signals into frequency information which is directly proportional to the speed of the material that passes the laser beams. The signal processor converts the information into speed information and updates the data for the user. The measuring unit measures the quantity of the reflected laser light to find out whether an object is in the measuring zone.
SOFTWARE FUNCTION AND VISUALISATION
AUTOMATIC CALIBRATION
The quality of the measured results mainly depends on the uniform conditions during the measuring process. Both measuring sensors are calibrated before each measurement to achieve high measurement accuracy.
For this purpose, a calibration sample is swivelled into the measuring range and an automatic calibration is carried out for both measuring sensors.
APPLICATIONS
TECHNICAL DATA
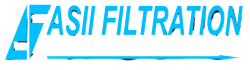