GreCon STENOGRAPH
Enabling inline raw density profile measurement with X-ray technology.
The development of the raw density profile is visualised in real time. Thus, the machine operator quickly receives reliable information that he can use for an optimum adjustment of the production process when, for example, starting up the line or changing the product. If irregularities occur, he can immediately take counter-measures. Production faults are detected and can be rectified in time.
A permanent monitoring and control of the raw density profile is part of the important parameters for a cost-optimised manufacture of wood based panels as the product properties of the wood based panels are decisively influenced by specific changes of the raw density profile.
Since the Stenograph does not need a cooling time – also not in continuous measuring operation – inconvenient “blind flights” do not occur during the otherwise usual switch-off phase.
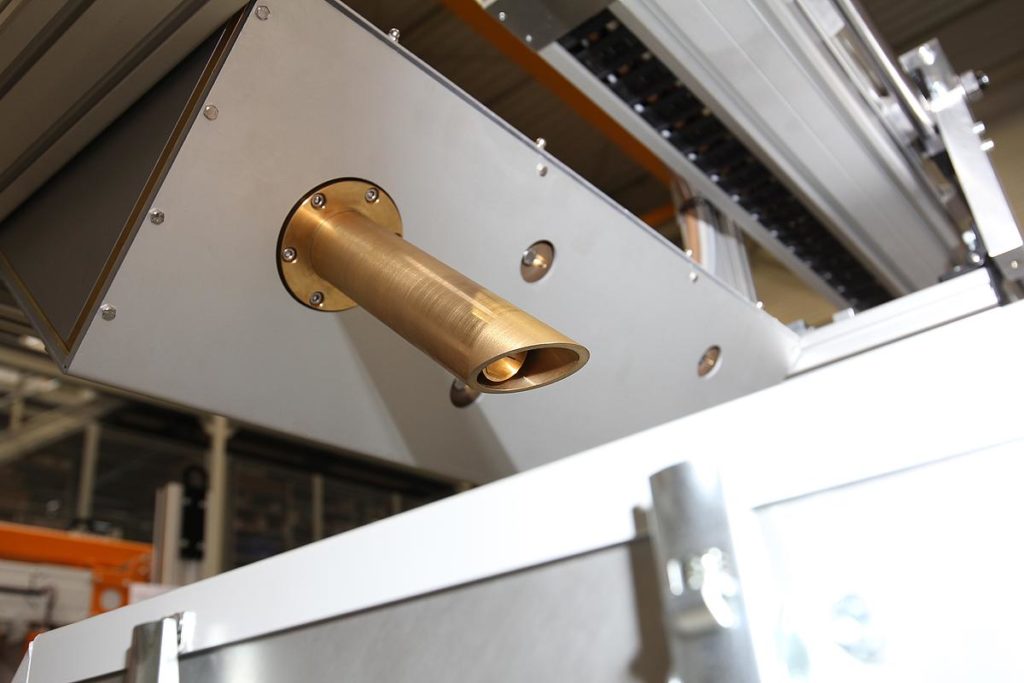
ADVANTAGES AT A GLANCE:
DESIGN OF THE SYSTEM
All ReceivingOPT products works with an standard measuring setup consisting of up to two NIR measuring heads, the central spectrometer unit (CSU) and an evaluation computer with the product software.The sensors of the ReceivingOPT BA were installed directly to the dumping site or bunker where the material will dumped through the truck. The ReceivingOPT BA-T 2.0 and ReceivingOPT BA-T 300 are stand-alone products which have the NIR measuring heads, the central spectrometer unit (CSU) and the computer inside the housing of the system. In the ReceivingOPT BA-T 2.0 the material is put in by the user and the system brings the material with a integrated screw conveyor over the NIR measuring head. The ReceivingOPT BA-T 300 has a integrated shredder which can shrink bigger particles of the material. The material sample will put into the system from the user. The System comes with calibrations for water content, ash content and calorific value. The standard calibrations are for the use with non-frozen materials. Calibrations for frozen materials available. Additionally, data can be exported as an Excel file or to a third party system using the data interface. It is also possible to integrate to an existing weighing software of e.g. a truck scale, in order to import the values into the BA-T system to complete the entry in the goods receipt book. Additionally, the systems can automatically send the daily journal to an e-mail distribution list.
MEASURING METHOD
The STENOGRAPH records the raw density profile contactless by means of X-radiation. The X-ray tube sends a photon ray through the panel in an angle of 45°. A detector 1 provided at the opposite side detects the transmitted radiation and a detector 3 which is vertically movable to the ray records the photons spread in the material. This movable detector 3 scans the panel from edge to edge to be able to record the entire profile. The denser the material, the less photons reach the detector 1 by transmission and the denser the point in the material recorded by detector 3, the more photons are spread in the material and detected by detector 3. The raw density profile course is calculated over the panel thickness by combination of the measured values that are detected. The data can be used immediately and result in savings with respect to the run-in times as well as to the material.
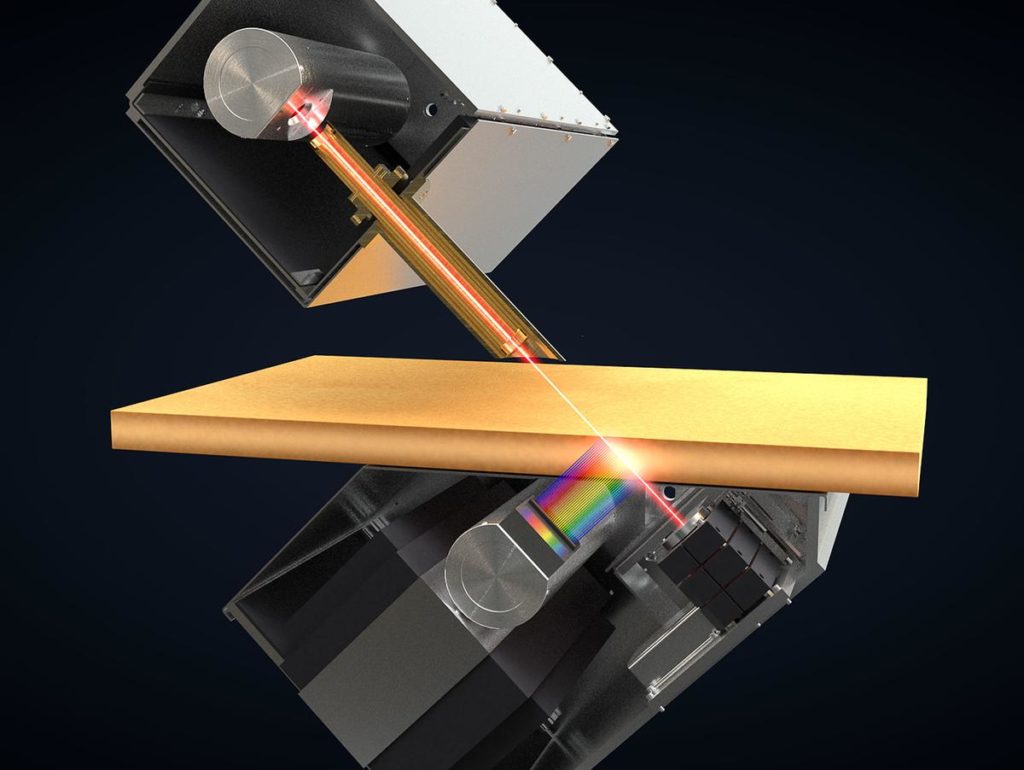
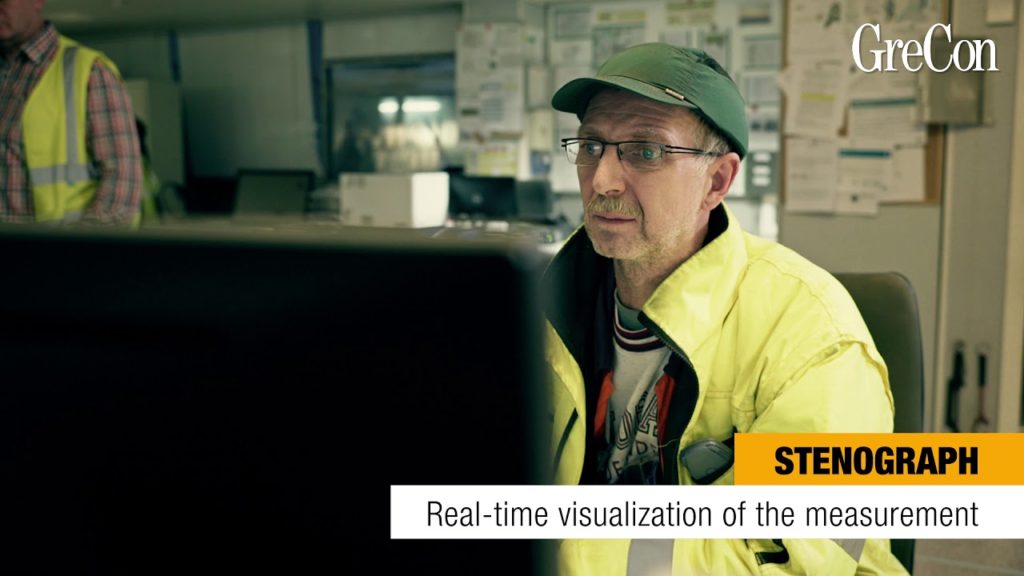
SOFTWARE FUNCTIONS AND VISUALISATION
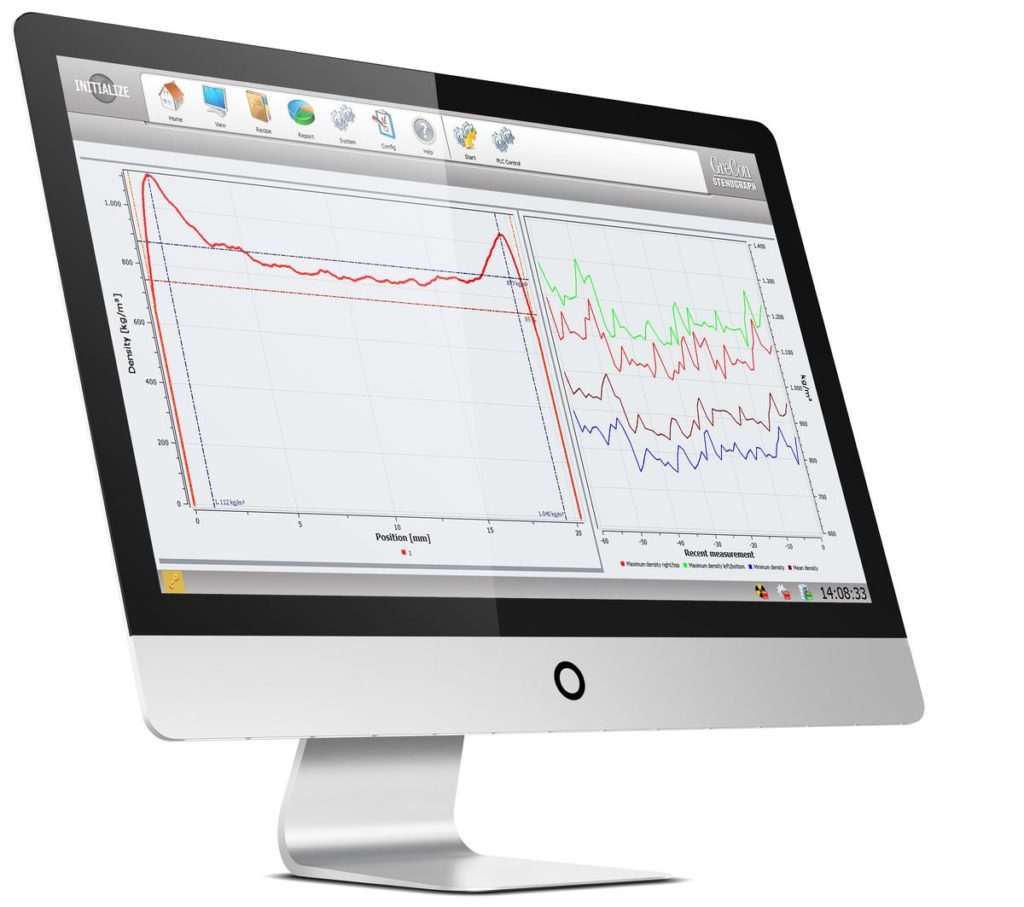
TECHNICAL DATA
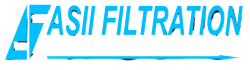